激光切割中的焦点位置检测方法研究
引言
激光切割加工具有切割精度高、切割速度快、热效应低、无污染、无噪音等优点,在汽车、船舶、航空航天和电子工业中都得到了广泛的应用。而激光切割加工质量与激光焦点与工件之间的相对位置有着密切的关系,保证激光焦点和切割对象之间的合理的相对位置是保证激光切割加工质量的关键之一。
激光聚焦的焦点位置无法直接测量,但可以通过间接方法检测。对于一个激光切割加工系统,其焦点位置是由聚焦镜的光学焦点决定的,所以在聚焦镜一定情况下其位置是不变的(不考虑聚焦镜的热效应),因此可以通过检测聚焦镜和被加工对象之间的相对位置来间接检测焦点和被加工对象之间的位置关系。
激光焦点和被加工对象之间的相对位置可以通过电感位移传感器和电容传感器来检测,在使用中各有优缺点。电感传感器的响应频率较低,不太适用于高速加工和像!维加工这样需要非接触检测的场合;电容传感器,具有响应速度快,检测精度高等优点,但在使用过程中存在非线性和易受激光切割加工过程中产生的等离子云和喷渣的干扰的影响。
本文将系统讨论激光切割加工中激光焦点位置误差的产生途径和自动消除误差的控制系统的组成。在此基础上分别讨论了两种传感器检测系统组成以及实际使用中存在的不足和克服的方法。
1 激光切割过程中焦点位置误差的产生
在激光切割过程中,产生焦点和被加工对象表面之间相对位置发生变化的因素很多,被加工工件表面凸凹不平、工件装夹方式、机床的几何误差以及机床在负载力下的变形、工件在加工过程中的热变形等都会造成激光焦点位置和理想给定位置(编程位置)发生偏差。有些误差(如机床的几何误差)具有规律性,可以通过定量补偿方法进行补偿,但有些误差为随机误差,只能通过在线检测和控制来消除,这些误差是:
1.1 工件几何误差
激光切割的对象为板材或覆盖件型零件,由于各种?因的影响,加工对象表面具有起伏不平,且在切割过程中的热效应的影响也会产生薄板零件的表面变形,对于1维激光加工,覆盖件在压制成型过程中也会产生表面的不平,所有这些,都会产生激光焦点与被加工对象表面的位置与理想位置发生随机变化。
1.2 工件装夹装置产生的误差
激光切割加工的工件是放在针状工作台上,由于加工误差、长时间与工件之间的磨损和激光的烧伤,针床会出现凸凹不平,这种不平也会产生薄钢板和激光焦点之间的位置的随机误差。
1.3 编程产生的误差
在1维激光切割加工过程中,复杂曲面上的加工轨迹是通过直线、圆弧等拟合的,这些拟合曲线和实际曲线存在一定误差,这些误差使得实际焦点和加工对象表面的相对位置和理想编程位置产生一定误差。而有些示教编程系统也会引入一些偏差。
2 激光切割过程中焦点位置在线检测与控制系统的组成
如图1所示,激光切割焦点位置在线检测与控制系统由控制器、检测系统、执行装置等部分组成。
独立式焦点位置检测与控制系统采用单独的坐标轴进行焦点位置误差的补偿控制,机械结构复杂,成本较高,但可与各种数控系统和激光切割机床配合使用。
而集成式采用激光切割机床本身的一个进给轴(对平面加工)或多个进给轴的合成(对于1维切割加工)运动来进行焦点位置误差的补偿。这种方式具有结构简单、成本低,易于调整等优点,但要求和数控系统统一设计,对数控系统的开放性要求较高。
2.1 电容传感器检测电路
如图2所示,电容传感器检测电路由调谐振荡器、信号放大器、晶体稳频振荡器、同步电路、混频电路、信号处理电路等将电容量信号变成对应频率的脉冲信号,通过对脉冲信号进行频率采样和处理,得到相应的电容量。这里的电容为切割喷嘴和切割对象之间两个极板形成的电容。显然其电容量除了与两个极板的面积有关外,还与极板之间的介质、极板之间的距离有关。而这个距离就与激光聚焦镜和工件之间的距离有关,也就是与激光焦点与工件之间的距离有关,所以电容量近似和焦点位置与切割对象之间的距离有关。这就是电容传感器检测焦点位置的原理。
2.2 电感传感器检测电路
如图3所示,由于采用了最新的大规模集成电路,电感传感器的检测电路比较简单,且集成电路采用了新的调制解调方法和算法,减少了以前的检测外差式调频检测电路方法由于传感器的激励信号的相角、频率以及幅值漂移对检测结果的影响,大大提高了检测精度和稳定性。
传感器信号通过处理后得到与传感器测头位移成正比的电压信号,通过变换电路转换成相应的频率信号,通过计算机处理得到了焦点的位置误差信号。
激光切割加工具有切割精度高、切割速度快、热效应低、无污染、无噪音等优点,在汽车、船舶、航空航天和电子工业中都得到了广泛的应用。而激光切割加工质量与激光焦点与工件之间的相对位置有着密切的关系,保证激光焦点和切割对象之间的合理的相对位置是保证激光切割加工质量的关键之一。
激光聚焦的焦点位置无法直接测量,但可以通过间接方法检测。对于一个激光切割加工系统,其焦点位置是由聚焦镜的光学焦点决定的,所以在聚焦镜一定情况下其位置是不变的(不考虑聚焦镜的热效应),因此可以通过检测聚焦镜和被加工对象之间的相对位置来间接检测焦点和被加工对象之间的位置关系。
激光焦点和被加工对象之间的相对位置可以通过电感位移传感器和电容传感器来检测,在使用中各有优缺点。电感传感器的响应频率较低,不太适用于高速加工和像!维加工这样需要非接触检测的场合;电容传感器,具有响应速度快,检测精度高等优点,但在使用过程中存在非线性和易受激光切割加工过程中产生的等离子云和喷渣的干扰的影响。
本文将系统讨论激光切割加工中激光焦点位置误差的产生途径和自动消除误差的控制系统的组成。在此基础上分别讨论了两种传感器检测系统组成以及实际使用中存在的不足和克服的方法。
1 激光切割过程中焦点位置误差的产生
在激光切割过程中,产生焦点和被加工对象表面之间相对位置发生变化的因素很多,被加工工件表面凸凹不平、工件装夹方式、机床的几何误差以及机床在负载力下的变形、工件在加工过程中的热变形等都会造成激光焦点位置和理想给定位置(编程位置)发生偏差。有些误差(如机床的几何误差)具有规律性,可以通过定量补偿方法进行补偿,但有些误差为随机误差,只能通过在线检测和控制来消除,这些误差是:
1.1 工件几何误差
激光切割的对象为板材或覆盖件型零件,由于各种?因的影响,加工对象表面具有起伏不平,且在切割过程中的热效应的影响也会产生薄板零件的表面变形,对于1维激光加工,覆盖件在压制成型过程中也会产生表面的不平,所有这些,都会产生激光焦点与被加工对象表面的位置与理想位置发生随机变化。
1.2 工件装夹装置产生的误差
激光切割加工的工件是放在针状工作台上,由于加工误差、长时间与工件之间的磨损和激光的烧伤,针床会出现凸凹不平,这种不平也会产生薄钢板和激光焦点之间的位置的随机误差。
1.3 编程产生的误差
在1维激光切割加工过程中,复杂曲面上的加工轨迹是通过直线、圆弧等拟合的,这些拟合曲线和实际曲线存在一定误差,这些误差使得实际焦点和加工对象表面的相对位置和理想编程位置产生一定误差。而有些示教编程系统也会引入一些偏差。
2 激光切割过程中焦点位置在线检测与控制系统的组成
如图1所示,激光切割焦点位置在线检测与控制系统由控制器、检测系统、执行装置等部分组成。
独立式焦点位置检测与控制系统采用单独的坐标轴进行焦点位置误差的补偿控制,机械结构复杂,成本较高,但可与各种数控系统和激光切割机床配合使用。
而集成式采用激光切割机床本身的一个进给轴(对平面加工)或多个进给轴的合成(对于1维切割加工)运动来进行焦点位置误差的补偿。这种方式具有结构简单、成本低,易于调整等优点,但要求和数控系统统一设计,对数控系统的开放性要求较高。
2.1 电容传感器检测电路
如图2所示,电容传感器检测电路由调谐振荡器、信号放大器、晶体稳频振荡器、同步电路、混频电路、信号处理电路等将电容量信号变成对应频率的脉冲信号,通过对脉冲信号进行频率采样和处理,得到相应的电容量。这里的电容为切割喷嘴和切割对象之间两个极板形成的电容。显然其电容量除了与两个极板的面积有关外,还与极板之间的介质、极板之间的距离有关。而这个距离就与激光聚焦镜和工件之间的距离有关,也就是与激光焦点与工件之间的距离有关,所以电容量近似和焦点位置与切割对象之间的距离有关。这就是电容传感器检测焦点位置的原理。
2.2 电感传感器检测电路
如图3所示,由于采用了最新的大规模集成电路,电感传感器的检测电路比较简单,且集成电路采用了新的调制解调方法和算法,减少了以前的检测外差式调频检测电路方法由于传感器的激励信号的相角、频率以及幅值漂移对检测结果的影响,大大提高了检测精度和稳定性。
传感器信号通过处理后得到与传感器测头位移成正比的电压信号,通过变换电路转换成相应的频率信号,通过计算机处理得到了焦点的位置误差信号。
1
2
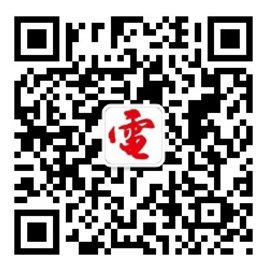
加入微信
获取电子行业最新资讯
搜索微信公众号:EEPW
或用微信扫描左侧二维码