纯电动汽车有一个传统方案无法解决的重量问题
纯电动汽车 (BEV) 有严重的重量问题,这种问题Weight Watchers®无法解决。
许多纯电动汽车比内燃机汽车 (ICE) 重33%。美国国家运输安全委员会主席指出:“福特F-150 Lightning比非电动版本重2000 到3000 磅。”另外,美国国家经济研究局 (National Bureau of Economic Research) 发现,车辆每增加1,000 磅,事故死亡风险就会增加约47%。
因此,汽车 OEM 厂商在尝试设计续航里程更长、安全性更高和电子内容更多的纯电动汽车时,面临严峻的限制条件。这是该行业有史以来面临的最严峻研发挑战之一。
尽管面临巨大的挑战,但如果电动汽车中的传统超重供电网络(PDN) 被48 V 区域架构取代,其中48 V 母线取代原有12 V 系统,则可减少OEM 厂商、消费者和立法者的这些担忧。部署由高密度电源模块支持的区域架构,将以3 种方式减轻重量。这种新架构将实现从粗线束到细线束的过渡,可将线束重量减少85%。此外,低压辅助电池可拆除并使用电源模块进行虚拟化,从而可完全消除电池重量。最后,使用电源模块进行PDN升级,可优化热管理系统,从而将其重量减少33%。
因此,采用分布式架构替代传统集中式架构 ,可显著减轻重量,还可提高整体电力系统效率。
1 采用48 V:对于纯电动汽车而言,是一项明显和期盼已久的改进在每个设计周期,新车都会增加安全、安防和自动
驾驶等新电子产品。每个额外的功能都会增加功耗,使用固定标准化电池已转化为电流的指数级增长。从电流趋势来看(图1),集中式架构PDN 是不可持续的。要恢复可持续电流水平并最大限度减少线束重量的同时,满足不断增长的电力需求,唯一的方法就是使用区域架构将工作电压提高至48 V。
图1 转换为48 V系统,会将车辆总电流从250 A 以上降至75 A以下,不会影响车辆电气性能。自1908年以来,随着汽车电子设备的增加,汽车电流需求已呈指数级增长。20世纪60年代,OEM厂商将电压从6 V提高到12 V,导致电流在60年首次减少。尽管现在需要更大的电流,但大多数OEM厂商仍然使用12 V母线。2023年,特斯拉成为首家宣布在整个汽车中全面采用 48 V母线的OEM厂商,这将大大降低电流需求。
当前的纯电动汽车由主高压电池(通常为400 V 或800 V)供电,不仅需要为电动牵引电机供电,而且还需要为大量低压负载供电,如空调、加热座椅和信息娱乐系统等。PDN 会将高压降至48 V 及12 V 辅助电池电压,为这些子系统供电。
根据欧姆定律,转而采用 48V 分布式架构将带来一个机会:。功率输出相同时,12 V 电源需要的电流是48 V 电源的四倍。因此,12 V 导线一般也比48 V 导线粗四倍。
2 12 V集中式架构的消亡
自20世纪60年代以来,12 V 集中式系统一直是汽车使用的传统电源架构。该架构由一个庞大的银盒外壳组成,其中包含一系列分立式组件,例如所有将高压(HV) 转换成48 V 至12 V 的DC-DC 转换器等。这个系统需要使用粗重的导线将12 V 电流传输至负载点。
此外,由于传统的DC-DC 转换效率低,这种集中式电源系统会从银盒产生大量热量,通常需要密集的液冷,这会增加更多的重量。
要过渡到48 V,可在端点位置使用高密度电源模块,以便在负载点高效转换为12 V。这使OEM 厂商能够随着时间的推移,高度灵活地逐渐将12 V 负载器件过渡到48 V。这有助于在对系统架构干扰最小的情况下,快速实现使用48 V 的优势。
3 48 V分布式架构降低热损耗、减少电流
这种新颖的48 V分布式架构系统利用了欧姆定律,是行业转变的典范,其中 DC-DC 转换发生在更靠近负载点的位置,而不是在中央银盒内完成。在该方案中,高压至48 V 的转换有助于将安全的48 V 用作整个车辆的母线电压。48 V 至12 V 的转换在负载点位置进行。通过48 V 而非12 V 传输电流,导线可以更细、更轻,很明显,成本也会更低(图2)。这种更细、更灵活的导线也更容易在车内布局。此外,这种方法可将与DC-DC 转换器有关的热损耗均匀地分布在整个车上,从而可使用安装在底盘上的热传导及空气对流散热系统的潜能。
图2 当今汽车有两种不同的PDN:12 V集中式架构和快速发展的48 V分布式架构。前者采用12 V粗线束,后者采用48 V细线束,细线束重量更轻,减少了热损耗,而且将电流降至1/4。
4 计算减少的重量
48 V 分布式架构不仅可更好地支持纯电动汽车日益增长的动力需求,同时还可采用3 种方法减轻汽车重量
1.线束:重量锐减约 85%
升级到48 V 分区架构,意味着传统的273 克/ 米的12 V、4 号电线将被27 克/ 米的48 V、10 号电线取代。这可减轻大约85% 的导线重量。
2.辅助蓄电池取消:重量减少~100%
电源模块的分布式架构可加速DC-DC 转换器的瞬态响应,从而创建虚拟电池。因此,12 V/48 V 分布式电源模块不仅可复制12/48 V 低压电池的特征,同时完全消除了物理12 V 电池,减轻了100% 的重量。
图3 电源模块可实现比12 V铅酸电池更快的瞬态响应,从而创建虚拟电池,可取代传统的笨重12 V电池。
5 电源系统优化:重量减轻约 33%
用区域系统取代集中式系统,可将48 V 至12 V 电源转换从银盒移至负载点。改进后采用高密度电源模块提供48 V 输出的电源系统盒将缩小达33%。因此,外壳重量可减轻多达三分之一(33%)。
在传统12 V 集中式系统中,分立式组件会在其银盒外壳内产生环境高温。采用高密度电源模块的电源系统盒产生的热量较少,而且负载点模块可在底盘上进行高效的通风散热。这些改进可使液冷系统瘦身 7%。
图4 使用电源模块和分布式架构时,可缩小集中式外壳,因为在48 V转换为12 V负载的端点可以更高效地散热。
6 化重量为机遇
OEM厂商可使用分布式架构获得各种优势。为了说明这一点,请考虑减轻重量对增加行驶里程的影响。车辆越重,能耗就越大,行驶里程也就越短。然而,如果将其用来增加电池尺寸,额外的重量就可降低对续航里程的影响。额外的电池提供更多的能量存储,可增加续航里程。
在Vicor 进行的一项研究中,高密度电源模块支持的分布架构可将车辆重量减轻40 磅(表1)。在该重量被40 磅的电池所取代时,在不增加净重的情况下,电动汽车的行驶里程每年可增加4000 英里。
表1 48 V分布式架构与高密度电源模块相结合,将使紧凑型电动SUV减重约18公斤(40磅)
这一点非常重要,因为美国联邦公路管理局2023年的数据显示,美国人平均每年开车的行驶里程为14263 英里。因此,使用48 V 分布式架构可减少每年30% 的充电时间(表2),并增加车辆一次充电的行驶里程。
表2 增加的行驶里程为司机增加了每次充电的行驶距离,减少每年所需的充电次数
7 创新消除重量顾虑
电动汽车超重,这种趋势既不能持续,也不利于电动汽车的整体发展。采用传统银盒和分立式组件的12 V集中式架构需要升级到48 V 分布式架构,以优化电动汽车的供电网络和散热管理系统。分布式架构可将每年的行驶里程增加4000 英里,也可用于实现额外的安全或电子功能。
最高效的区域架构在负载点使用小型轻量级转换器。高效的高功率密度模块是48 V 至12 V 转换的最佳选择。
鉴于当前复杂的汽车电力电子产品,OEM 厂商不仅需要创造性地减轻重量,同时还需要提高性能。Vicor是高性能电源模块的领导者,始终致力于实现创新和创造。Vicor 紧凑型电源模块、架构和拓扑为汽车OEM 厂商提供高度灵活的可扩展电源解决方案,用于整个车辆的高压电源转换。易于部署的电源模块是原有集中式电源系统使用的传统分立式设计的替代方案。此外,小巧紧凑的电源模块也是48 V 区域架构显而易见的选择及合理补充,48 V 区域架构是汽车行业供电网络的未来。
Weight Watchers®是WW International, Inc.的注册商标。Vicor是Vicor公司的注册商标。
(本文来源于《EEPW》2024.1-2期)
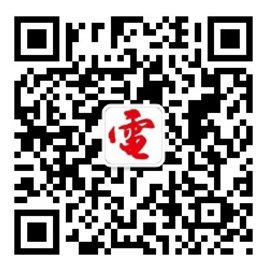
加入微信
获取电子行业最新资讯
搜索微信公众号:EEPW
或用微信扫描左侧二维码