底盘系统零件的振动性能优化技术
引言
汽车的行驶平顺性以及声学性能的改进,除了需要花费精力对组成系统的单个零件进行细致的分析设计之外,更重要的是需要对整个悬架系统以及组成系统的零部件之间的相互作用进行精确研究。通常,由于对单个零件在系统性能中的影响估计不足,有些公司在花费大量的人力物力对悬架或阻尼系统元件进行单独研发后,得到的系统性能却不尽如人意。
威巴克公司作为全球汽车工业领域内振动和声学控制技术的领先者,在多年的产品研究和开发实践中积累了丰富的经验,形成了自己独特而有效的产品开发体系。在威巴克公司,无论是开发新的汽车底盘零件或是对现有底盘零件进行性能优化,总是先从整体上对汽车子系统的振动性能进行研究,识别现存的性能改进空间,然后再通过零件设计技术对单个产品的性能进行优化,最终通过多个阶段的测试来验证所开发的零件成功与否。
零件开发及试验验证技术
基于台架试验研究所获得的详细的系统特性信息,可以用来建立计算机模拟模型。模型包含了所有悬架元件,还有控制臂或连接杆件,有时还会包含具有理想刚性的副车架,元件之间通过耦合元件或力单元相互连接(见图1)。模型通过对舒适性有影响的零件特性参数来描述。通过开关变量来控制被模拟零件的开或关,以便对比试验结果和计算结果,分析零件对系统性能的影响以及估计解决方案对系统性能的改进空间。系统中的每个零件都可用具有理想特性的元件替代进行性能贡献分析,以评价它们各自对系统性能的影响。被优化零件的性能改进空间则可以通过初始状态和理想状态下的性能对比来估计。将贡献分析和性能改进潜力分析技术相结合,可以大大节省设计成本。贡献分析完成后可以确定主要的被优化零件,例如,充液减振器活塞连杆的摩擦力是小激励下寄生刚度升高的主要来源,但用一个价格昂贵的低摩擦减振器来替代它并非绝对必要,通常为现有减振器匹配一个改进后的顶部支撑就可以达到所需的舒适性效果。
汽车的行驶平顺性以及声学性能的改进,除了需要花费精力对组成系统的单个零件进行细致的分析设计之外,更重要的是需要对整个悬架系统以及组成系统的零部件之间的相互作用进行精确研究。通常,由于对单个零件在系统性能中的影响估计不足,有些公司在花费大量的人力物力对悬架或阻尼系统元件进行单独研发后,得到的系统性能却不尽如人意。
威巴克公司作为全球汽车工业领域内振动和声学控制技术的领先者,在多年的产品研究和开发实践中积累了丰富的经验,形成了自己独特而有效的产品开发体系。在威巴克公司,无论是开发新的汽车底盘零件或是对现有底盘零件进行性能优化,总是先从整体上对汽车子系统的振动性能进行研究,识别现存的性能改进空间,然后再通过零件设计技术对单个产品的性能进行优化,最终通过多个阶段的测试来验证所开发的零件成功与否。
零件开发及试验验证技术
基于台架试验研究所获得的详细的系统特性信息,可以用来建立计算机模拟模型。模型包含了所有悬架元件,还有控制臂或连接杆件,有时还会包含具有理想刚性的副车架,元件之间通过耦合元件或力单元相互连接(见图1)。模型通过对舒适性有影响的零件特性参数来描述。通过开关变量来控制被模拟零件的开或关,以便对比试验结果和计算结果,分析零件对系统性能的影响以及估计解决方案对系统性能的改进空间。系统中的每个零件都可用具有理想特性的元件替代进行性能贡献分析,以评价它们各自对系统性能的影响。被优化零件的性能改进空间则可以通过初始状态和理想状态下的性能对比来估计。将贡献分析和性能改进潜力分析技术相结合,可以大大节省设计成本。贡献分析完成后可以确定主要的被优化零件,例如,充液减振器活塞连杆的摩擦力是小激励下寄生刚度升高的主要来源,但用一个价格昂贵的低摩擦减振器来替代它并非绝对必要,通常为现有减振器匹配一个改进后的顶部支撑就可以达到所需的舒适性效果。
图1 多体系统动力学模型
图2 车桥试验台架
1
2
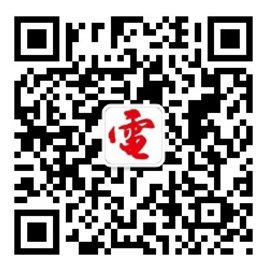
加入微信
获取电子行业最新资讯
搜索微信公众号:EEPW
或用微信扫描左侧二维码