表面微观结构二维测量和三维测量的应用分析
至於对连杆大头孔内壁的评定要求,眼下多数国内企业还只采用Ra或Rz,且通过调研发现,所设定的指标值的分散性还较大,如在以Ra为评定参数时,从Ra0.2、Ra0.3到Ra1.6、Ra2.0都有。可见此时对孔壁微观结构的要求还是较宽松的。但如前所述,随着近年来产品结构和工艺的改进,对连杆大头孔内壁的微观结构要求也在提高,以下表述的要求有一定代表性:1.Rz A±a;2.Rpc minn(±C)。
第一项评定参数Rz的值已不同於习惯表示,而是要求R保持在一定范围内,以确保被测表面必须“粗糙”到一定程度。另一项评定参数为Rpc(有时也被称为PC),即“标准化的轮廓波峰统计”,也可简称为“波峰计数(Peak Count)”,即在评定长度内,超过了所设定的统计边界上限和下限(C1,C2)的波峰和波谷的数目,参见图3。
图3 三种常选的沟槽造型结构示意
Rz=(8±3)μm
取样长度0.8mm,评定长度4mm
Rpc min =170/cm
统计边界 ±0.3μm
实际进行粗糙度测量时,仪器只经过4mm的评定长度,但在评定时,需转换到10mm的标准距离,并要求≧Rpc 170,而统计边界为±0.3μm。
激光造型工艺与成型表面的特点
激光造型作为一种新工艺,直到本世纪初才在其诞生地—汽车工业强国德国的少数企业得到实际应用,但在用於发动机汽缸体缸孔和连杆大头孔精加工等关键工序的实践中,已经充分显示了这种先进技术的很大优越性。近年来,激光造型在欧洲汽车发动机业界的应用日益增多,并自2009年开始,进入了国内的主流汽车发动机生产企业,展现了它十分广阔的巿场前景。
简单地说,这项新技术就是利用激光头所发出的数控激光光束在被加工表面制作出符合事先设定要求的表面微观结构的一种工艺方法。在实施表面造型的加工过程中,高能量的光束将有部分被工件表面反射、有部分则被吸收,被吸收的光束能在瞬间将材料加热并使之达到气化状态。这种“激光刀”产生的光束的切削能力取决於脉冲频率、功率、开关时间和进给速度等。由於温度升高是瞬间产生的,并且具有很高的能量聚集密度,因此光束只在一个有限的局部做瞬间切削,工件材质的特性不会由此而产生变化。另一方面,粘结在工件表面上的冷却剂残余物将被蒸发或燃烧,也不会影响到激光光束切削的质量。专用造型设备的数控系统能驱使激光头做上下和旋转运动,并对光束的开关时间和能量进行相应的控制,从而使用户能获得不同要求的、可控的表面微观结构。
对於缸孔精加工工序而言,最终获得的理想表面,应该是一个既有较高光洁度的平台结构,又具有可控的、适量而又充足的微观构造,以使机油有较长的驻留时间和良好的流体动态压力。为此,在引入了这项新技术後,选择的是规整、均匀的沟槽方案,具有交错断续或交叉点坑的分布特徵。图3是常选的三种沟槽构造形式:袋状(左)、杯状(中)和块状(右)。上述结构的一个共同点是无交叉、不连通,各沟槽相互之间没有任何联系,能有效存储润滑油而不易流失,便於形成均匀油膜,使摩擦付处於流体润滑状态。由此,既保证了足够的润滑,又阻止了过多的机油窜入燃烧室,还可减少应力影响,对改善摩擦性能有很大好处。相比之下,传统珩磨工艺在缸孔内表面形成的往往是相互连通的网状沟槽结构,且表面粗糙度偏“粗”,导致储油量过多。而采取镭射造型工艺的结果是使润滑油的消耗量会有较大幅度的减少,涉及环保的指标,如颗粒物排放和油粒排放则有明显降低。图4是采用这项新颖工艺加工的缸孔的实况,从图中可见,真正实施镭射造型的只是位元於承受高负载的缸孔上死点附近进行的区域,以保证活塞环在该区域受到高负荷时的良好润滑。
图4 采用激光造型工艺加工後的缸孔
图5 大头孔圆周上的造型区
通过以上介绍可看到,经激光造型形成的工件表面微观构造,与传统的工件经切削加工後的成型面有很大差别,最大的不同是後者为连续性的纹理结构,而前者则具有断续性、不连贯的特徵。两者之间的这个差别导致在进行检测和评定时,若还是把二维测量、评价的方式用於执行镭射成形的工件表面就会产生较大误差。一个显见的事实是,如前所述,对工件加工面的技术要求,在若乾重要部位还需满足相关工艺性能,指的都是配合面。 因此在理论上,当进行检测和评价时也应该把“面”作为对象,之所以无论国内还是国外一直沿用二维测量方法,正是利用了传统切削加工形成的工件表面所具有的这种连续性纹理结构特徵,而采取的一种“简化”方案。
图6 经激光造型後的工件表面示例
如图中显示的状态,所得到的结果应该是相同的,这只要从对应於下方的二维测量截线就能看出。而事实上,即使就取图中这一块平面来看,左边的袋状构造较之右边的杯状,其储油空间要大的多。
即使是对同一个表面,只要稍稍移动一下测针的测量轨迹,也会得出完全不同的结果。设想把左(或右)图中的红线稍稍下移,就会造成只测到一个沟槽、甚至测不着的情况,从而得出与图6完全不一样的评定结论,显然以上者两种情况都说明,此时若再沿用二维测量方式是不可行的。
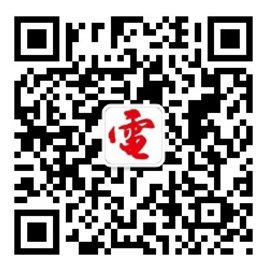
加入微信
获取电子行业最新资讯
搜索微信公众号:EEPW
或用微信扫描左侧二维码