基于FPGA和NiosII的逆变焊接电源控制器
3 仿真与实验
3.1 ADC控制器仿真
ADC控制器可以使用QuartusII自带的SignalTapII逻辑分析仪进行仿真验证。SignalTapII逻辑分析仪可以直观地观测ADC控制器采集到的当前ADC的转换结果,准确而高效。为了加快仿真速度,对ADC的转换值不加滤波处理;为避免最低位剧烈抖动,仿真时仅仅采用高12位,去掉最低两位的结果。参考电压5 V,将电压通道接到了模拟地(理论值为0000h),电流通道连接到2.54 V左右的模拟电压(理论值为0820h)。 SignalTapII仿真结果如图7所示。
可见,所设计的ADC控制器能够稳定地控制AD7863工作,除了稍有抖动之外(未加滤波环节),采样结果准确可靠。
3.2 DPWM控制器仿真
为了验证所设计的DPWM控制器是否合理,在保证仿真有效的前提下做如下约定:保护清除按键和DPWM启动按键信号均以直接数字量置位来代替;将算法输出信号ALG_IN视作给定;反馈电流数字量设为恒值500;死区时间设定为3.0μs,最小脉宽占空比为2.4%。
仿真环境为QuartusII-7.2,仿真结果如图8所示。启动信号STRT有效之前DPWM输出全部封锁,输出均为低电平;STRT有效后,在给定小于最小脉宽时输出最小脉宽,随着给定的增大,脉宽变大;当检测到过流信号(OV_C)时,4路DPWM输出立即置低(即全部被封锁),且置低状态能一直持续到保护信号PRTCT_CLR清除后才结束。可见DPWM的输出严格受控。
3.3 焊接试验波形
3.3.1 静态负载焊接试验
在静态负载条件下,NioslI通过DPRAM给定定频100 Hz和带后中值的脉冲电流。电流脉冲参数为:峰值300 A,峰值时间4 ms;中值100 A,中值时间1 ms;基值电流30 A。采用6段PID参数。实际输出的电流和电压波形如图9所示。
图9中,上面为通道1,波形为输出电流,每格1 V,代表实际焊接电流100 A;下面为通道2,波形为输出电压,每格1 V,代表实际焊接电压10 V。可见,焊接电流波形与给定的脉冲波形(如图3所示)基本一致。
3.3.2 动态负载焊接试验
双闭环控制策略下,死区时间3.0μs,最小脉宽占空比为2.4%。电流脉冲参数为:峰值450 A,峰值时间3 ms;中值150 A,中值时间2 ms;基值电流50 A。6段PID参数。给定平均电弧电压为30 V,保护气体成分为20%CO2+80%Ar,保护气体流量为25 L/min,碳钢焊丝直径为1.2 mm,送丝速度为4.5 m/min。试验结果表明,当焊枪大范围抖动时,为了调节电弧的平均电压以保证焊接电弧稳定,电源系统实时地稳定电弧,且电流脉冲的频率变化均匀,峰值、基值分别随焊枪的抖动而上下微调。
4 结论
本设计采用FPGA+NioslI软核为控制核心,设计了全数字化脉冲MIG逆变焊接电源控制器。试验结果证明:数字化的设计思路增强了系统的稳定性和灵活性;一块FPGA在保证控制器功能的前提下,大大降低了开发成本,缩短了开发周期;在FPGA内部实现6段变参数PID以及改进的I-I电流-电弧双闭环的控制策略,脉冲电流跟踪效果良好,焊接电弧调节稳定,动态性能良好,实际焊接效果出色。本设计的核心逻辑都是基于统一性较好的VHDL语言设计,并采用模块化的设计方案,因此便于推广和移植。
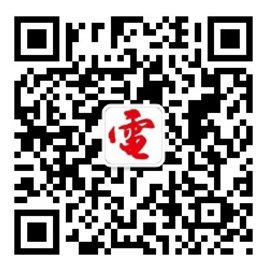
加入微信
获取电子行业最新资讯
搜索微信公众号:EEPW
或用微信扫描左侧二维码