走进GE可再生能源工厂 数字化带来巨大效益提升
高端仪器本土制造
巧合的是,在这家工厂对面,就是GE医疗天津工厂——GE美国以外唯一生产核磁共振、包括所用超导磁体等相关医疗影像产品核心部件的基地。
此前GE中国区总裁段小缨接受本报记者专访时表示,将会持续推进GE中国的数字化和本土化。而这两大战略在GE天津医疗工厂中有着明显的体现。
据介绍,GE医疗天津生产基地生产的磁共振相关设备,产品发往全球数十个国家,2015年产值达1亿美金。而天津工厂有100名员工,其中超过80%为当地培养的人才。
“除了人才的本土化,设备制造的本土化之外,我们还会继续推进本土化的战略。” 天津工厂高级工程师邱元元说:“目前,我们设备制造所使用的原材料,也有47%以上来自中国的供应商。”
除此之外,以新光纤MR和螺旋MR为代表的1.5TMR系统由GE中国团队研发设计,可以提高30%信噪比,实现2.0T图像效果。截至2015年,产量超过500台,其中70%远销全球市场。
截止目前,由天津生产基地组装测试的核磁共振系统占中国市场销量的65%,占全球市场销量超过50%。此前段小缨向记者介绍:“全球每四台新出货的核磁共振设备,就有两台来自中国。”
邱元元告诉记者,该工厂已经开始使用基于predix的GE数字工厂应用,“这些数字化的应用为我们带来的效益超过20%。”
在GE天津工厂的一台绕线设备上,装有数个传感器同时工作。“这些传感器监控超导磁体的绕线工作,包括其速度、张力、密度等多个指标。”邱元元介绍,“这些数据会同步上传到我们基于工业互联网应用平台Predix的应用上。”
说着,他拿出手机打开了一个应用,向记者详细介绍应用上的参数:“这些都是工厂在生产中的实时数据,这些数据帮助我们分析目前绕线机器的生产状况,如果有问题这些应用就会自动调整。”
不过他也向记者坦承,由于数字化生产和工业互联网的推动,对于人才和团队的要求更高了。一个应用于工业生产的应用,需要同时由程序编写人员、算法设计人员、医疗制造专业人员和工人等一起研发,哪一方面人才的缺少都会对研发工作形成掣肘。“我们也在不断摸索的过程中进步。”他说。
忠旺“上位”
中国企业也在奋力追赶。在远离上述两家企业50公里外的武清经济开发区,一家年设计产能180万吨的铝材压延生产线正在试运行。
这条生产线属于中国忠旺控股有限公司天津工厂,在记者到访该工厂的前一天,中国铝行业最大的一笔海外收购交易落地。忠旺美国与全球顶尖的高端铝压延产品研发制造商爱励铝业有限公司签订了23.3亿美元的收购协议。
天津忠旺常务副总经理李庆江告诉记者,天津工厂所用的铝材压延生产线的全部大型设备,均从国外进口,其设备之间的配合绝大部分依靠自动化控制系统,智能化程度之高为世界前列。
在高度自动化的生产系统支持下,工厂所使用的人力相对减少。铝材压延生产流程中,最开始的步骤是将原铝与其他金属元素混合,熔炼成铝合金。而在熔炼车间内,巨大的厂房中仅有40余名工人进行设备操作。
“包括合金元素的配比、温度的调控、废料的收集等,全部都是依据设备开始设定的程序进行工作,工人所做的就是监控和简单的操作。”车间负责人告诉记者:“智能化不仅提高了工作效率,也减少了人为操作失误导致的生产事故。”
而这样的自动化在提高生产效率的同时,也大大提升了产品的质量。目前,忠旺天津工厂熔铸车间生产出宽幅为2670mm的铝合金铸锭,创中国纪录;热轧车间轧制出宽幅为4300mm的铝合金板材,创亚洲纪录。天津工厂还一次性通过三项质量管理体系认证,取得包括航空及汽车行业的管理体系证书,为产品进入高端领域打下基础。
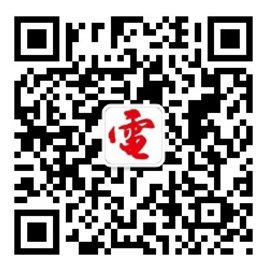
加入微信
获取电子行业最新资讯
搜索微信公众号:EEPW
或用微信扫描左侧二维码
相关文章
-
2019-03-26
-
2018-12-26
-
-
2018-09-13
-
-
-
-